Nothing like a bit of a stoush to stimulate my education. As one of the moderators, I have decided to put everything into perspective to avoid any genuflexing. Tim's question has raised a point that Albert really did not cover in his excellent posting, and that is the rear part of the air compressor crank and its lubrication and sealing. The mechanics among you who already know all this do not need to read further. This is written for the mechanically ignorant like me.
Firstly, to follow up on my last post, the price of 001 997 72 45, the O ring between the air compressor and the power steering housings is $5.50 retail. Now to how a moderator will deal with this issue. Firstly, go into the garage and get a few examples of the items under dispute. Take an intact pair and pull them apart to demonstrate that the moderator is not biased and not a magician. This pair are clearly not from a 6.3, but they will do for the sake of the argument.
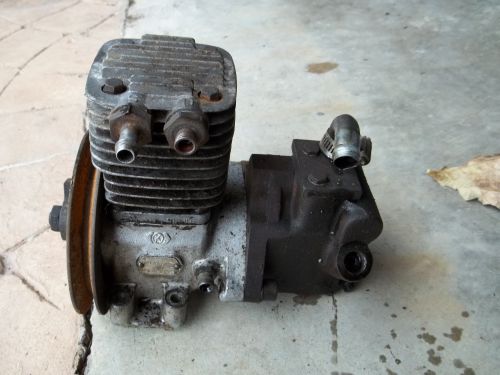
Take trusty Allen Key wrench and separate the two components in question.
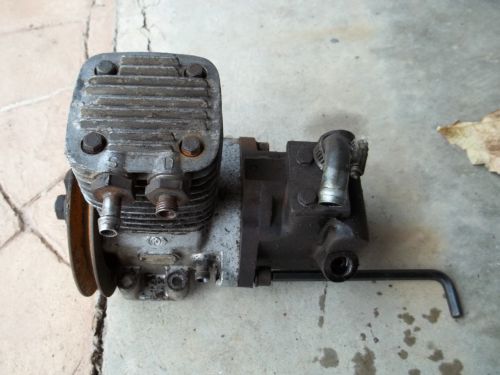
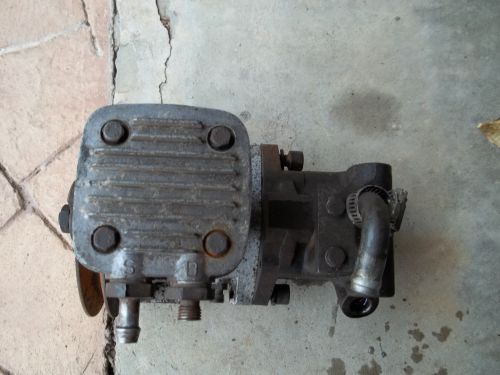
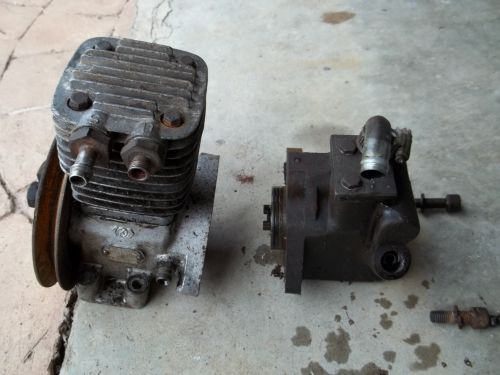
Now here is what you see if you look at the front of the power steering pump.
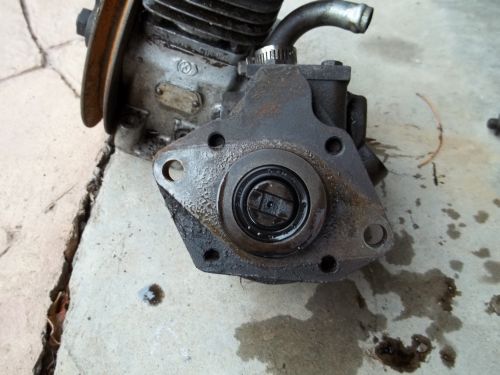
Here is a different one off a 6.3 to show they are the same. The radial seals are "shot".
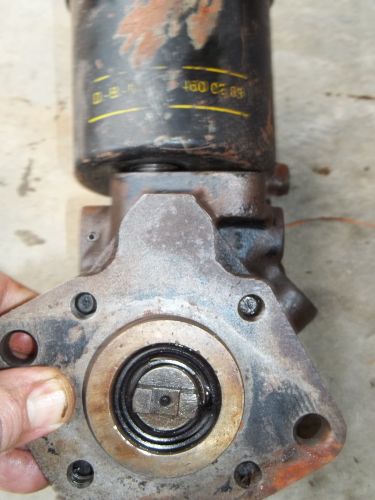
I believe that the rubber seal around the drive shaft is the radial seal/lip seal that Tom Hanson and Ron are talking about - Ron, correct me if I am wrong.
Here are a couple of angled views showing 001 997 72 45 which is flattened by use and age. This seal between the two housings stops oil around the drive coupling from leaking to the outside world.
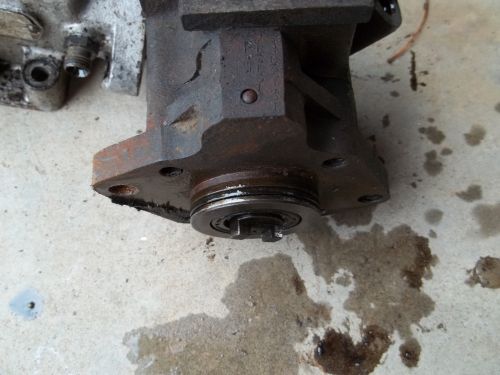
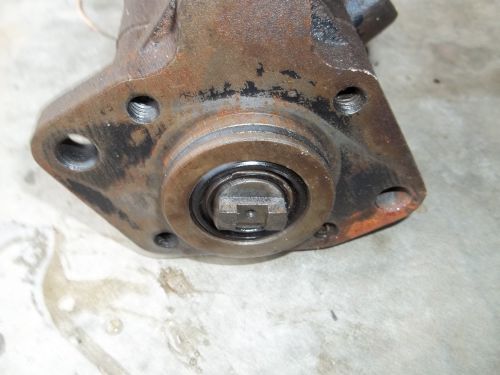
The radial seal prevents oil around the coupling and power steering fluid in the power steering pump from mixing. I have no idea which would be at higher pressure and shall not get into that argument, because I would not have a clue.
Now here is the rear of the air compressor, an area only shown once in Albert's pictures as pointed out by Kai amd previously noted by me when I also looked for the same reason.
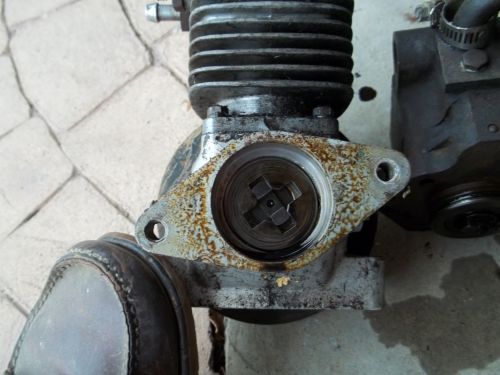
There is a drive coupling between the two shafts which obscures the view.
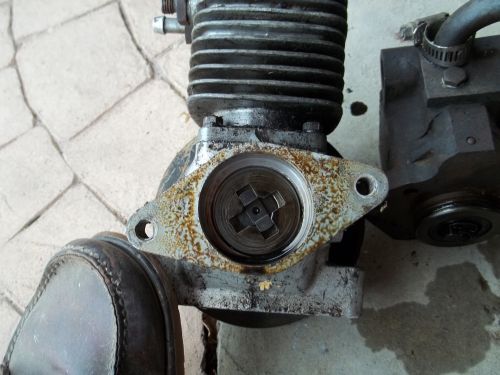
So, I have taken it out.
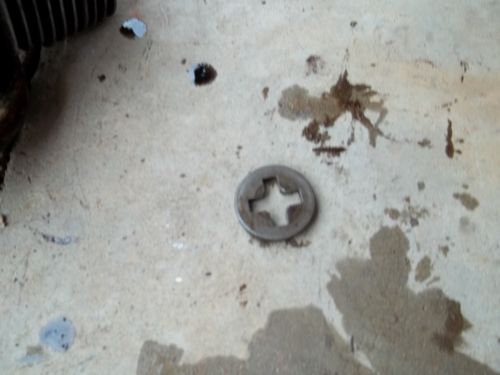
Now you can see the rear of the crank in its bearing shell and the oil return hole that Chris is talking about on the right hand side, and I'll come back to that later.
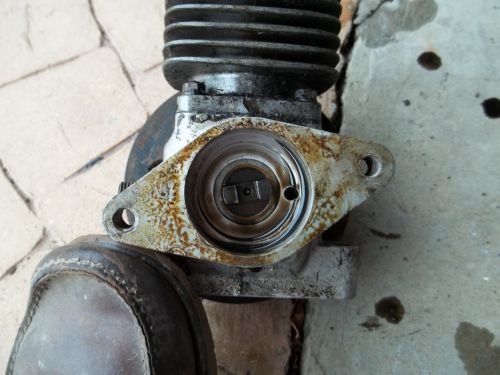
Here is a similar air compressor pump body (sump) with the crank out.
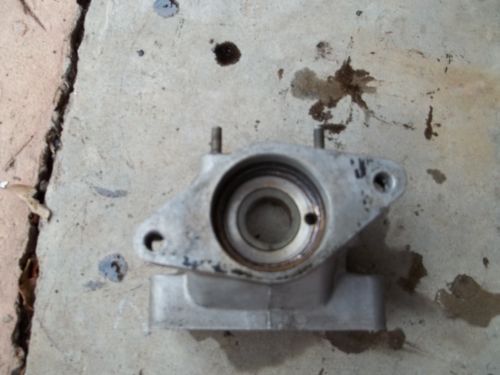
Here we are looking at the bottom of the air compressor sump to show the large drain hole for the sump oil with its surrounding O ring for return of the air compressor sump oil to the engine sump via the hollow mounting bracket that the air compressor sits on.
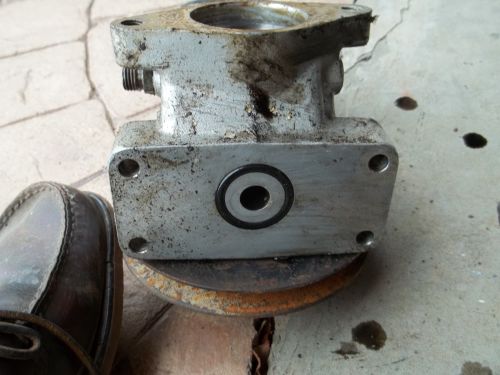
This picture shows an outide view of one of these air compressor sump bodies and you will notice that the high pressure oil feed line from the top of the oil filter on this body is on the opposite side to where it is in the 6.3 and 600, explaining one reason why M-B list more than one version of the air compressor. The one I pulled apart for this dissertation is similar.
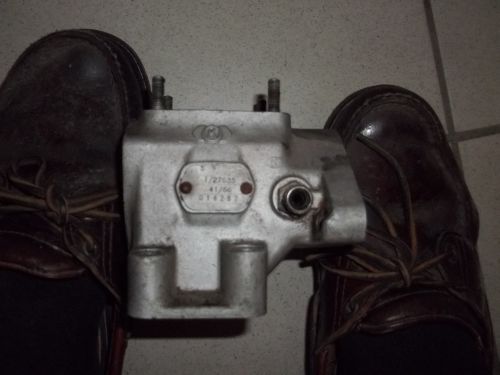
Now this is what I found interesting. Knorr who make these pumps don't make a different casting for the sumps for inside or outside feed, they make the housing so it can be drilled and tapped from either side to reach the rear crank bearing.
So the high pressure oil input to the air compressor sump feeds to a circular groove in the housing where the rear bearing is mounted. From there, it feeds through 3 small holes in the bearing shell, set at 120 degrees apart. This is the same type of lubrication used in the fan coupling that Justin and I rebuilt off the M189 and used elsewhere. If these tiny holes or the circular groove become plugged with rubbish, the lubrication of the pump crank will fail. I don't think Albert covered this. The same would apply if the channel between the holes in the crank shaft bearing surfaces became blocked. I could not see any other holes for entry of oil into the air compressor sump from the high pressure line.
You can see one of the 3 holes here at 12 o'clock.
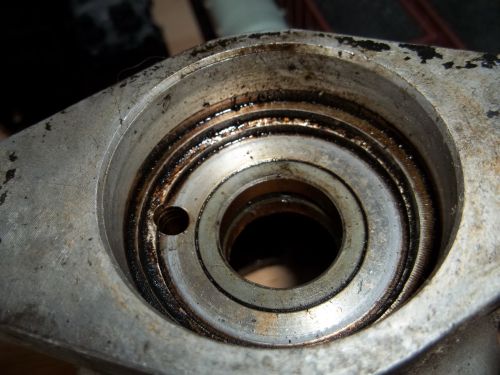
And by turning the housing upside down, the other 2 here at 10 and 2 o'clock. Note also the groove in which these holes lie which lines up with the small hole in the rear bearing face of the crank shaft.
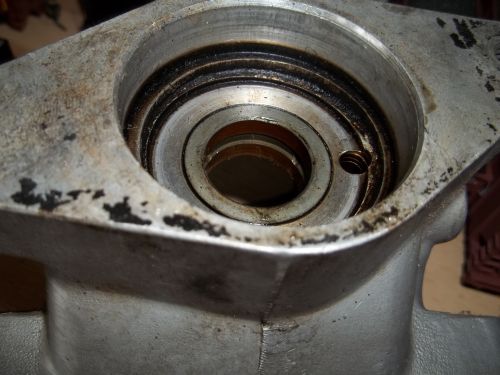
So, unless I missed something (which is quite possible), the oil all feeds in via this route and can spread equally either forward through the hole in the crank into the sump via the front bearing surface or rearward into the coupling housing. That which feeds rearward returns to the sump via the large hole set at 3 or 9 o'clock, depending on whether the feed line comes from the outside of the pump or the inside respecively. The hole is opposite the side of the inflow fitting and channel to the bearing. To my mind, the position of this hole would mean that the coupling housing would always be half full of oil, whereas, the sump itself would have very little oil because its drain is in the middle of its bottom side.
Here are a couple of air compressor housings to show the opposite set up of the oil input line and drain holes.
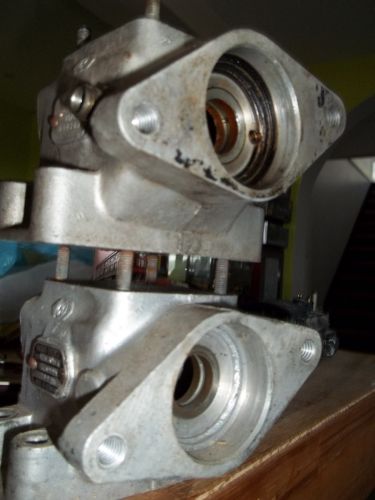
So, in a sense, Chris is totally correct in saying "There simply is no seal on the rear of the compressor." But, if you count the coupling chamber as part of the compressor sump which it is from the oil's point of view, then the seal that Ron is talking about is between the compressor and the PS pump. Strictly speaking, it is in the front of the PS pump, not in the air compressor, but it is in direct contact with the air compressor sump oil. The front of the PS pump acts as the rear of the air compressor in this set up where the PS pump drive is from the rear of the air compressor, otherwise oil would just spew out everywhere because there is no back wall on the air pump over the rear bearing.
Did I get this all right and does it settle the argument?
[:)]Art